Signs you are in need of a new roof
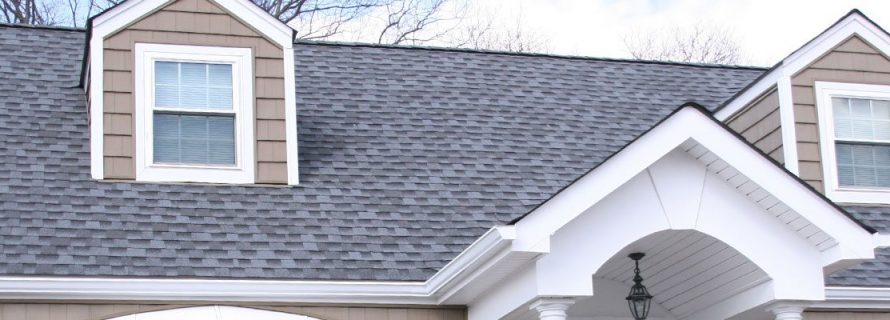
ALGAE
Algae growth causes a dark discoloration on roofs. The algae is usually brown to black in color which results in a streaked, dirty looking rooftop. It can be mistaken for soot, dirt or tree droppings, which typically produce only localized discoloration. It’s caused by the growth of air-borne algae which deposits on your roof. The good news is that algae growth does not affect the service life of your roofing material. It occurs most often in warm, humid climates such as the Southeast (where algae-resistant shingles are available).
Recommendations
- Discoloration of roofs caused by fungus or algae is difficult to remove, but may be lightened by spraying a diluted solution of chlorine bleach, trisodium phosphate, and water onto the roof. Solutions range from one cup TSP, one gallon bleach and four gallons of water, to one cup TSP and 2.5 gallons each of bleach and water. This solution can then be rinsed from the roof in 10 to 15 minutes. Do not scrub. Scrubbing will loosen and remove granules. After spraying be sure to thoroughly flush the roof and the greenery around the home (grass, bushes and shrubs) with water. The effectiveness of this type of cleaning may only be temporary, and the discoloration may recur. High pressure washing is not recommended due to the possibility of removing granules, thereby shortening the life of the Roofing System.
- For a more permanent solution, re-roof with Owens Corning Algae-Resistant Shingles. They are specifically designed to inhibit most algae growth for extended periods of time and are backed by our strongest product and algae resistance warranties* available to homeowners.
*See actual Algae-Resistant shingle warranty for details. Algae-Resistant products are not available in all areas. Contact your local Owens Corning supplier for more information.
DAMAGED FLASHING
Causes
Improper installation on a new roof
Drying and cracking on an old roof
Dented by improper nailing
Settling of the structure
Recommendations
- In most cases it is only necessary to remove and replace the flashing and shingles around the damaged area.
BUCKLING
Causes
Improperly applied felt
Wrinkled underlayment
Roof deck movement
Spacers not used in between roof deck boards
Poor roof ventilation
New shingles applied over old, rough shingles
Recommendations
- Allow moisture to escape the Roofing System. This can be a slow process and could take until the following spring. Once the Roofing System reaches the proper moisture content, the roof should lay flat and the buckling problem should not return.
- Remove the shingles that are affected. Cut the wrinkle in the felt and replace the shingles.
- Add ventilation to the attic space. The minimum requirement is one square foot of net free vent area per 150 square feet of attic floor space if a vapor retarder is not present. If a vapor retarder is present, the amount of required ventilation can be reduced to one square foot of net free vent area per 300 square feet of attic floor space.
- Consult the services of a professional. Make sure to apply shingles in accordance with the shingle manufacturer’s recommendations.
CURLING
Causes
High nails
Lack of back coating
Under-saturation of asphalt felt in organic shingles
Lack of ventilation
Improper number of fasteners
Recommendations
- Check location and number of fasteners
- Added roof ventilation can often correct
BLISTERING
Causes
Moisture in the shingles
Recommendations
- If the blisters break open revealing the asphalt, the affected shingles should be replaced.
- Consult with the manufacturer of the shingles.
MISSING SHINGLES
Causes
Improper fastening
Exposure to high winds
Recommendations
- Replace shingles which have completely blown off. For shingles with tabs blowing up and down, hand seal the shingles with an asphalt plastic cement, commonly referred to as flashing cement. This roofing cement must comply with ASTM D4586 — Type I or Type II which is the standard specifically for asbestos-free asphalt plastic roof cement. (Some products meeting this standard may involve hazardous materials. This bulletin does not purport to address all of the safety and health problems associated with the use of materials meeting this specification. It is the responsibility of the user to observe the safety and health practices as determined by the manufacturer of the product and stated on the label, instructions and Material Safety Data Sheet (MSDS).
- To hand seal, lift each tab of a 3-tab shingle and apply two spots of the cement under each tab. Each spot should be approximately the size of a quarter and placed 1″ to 2″ from each end of the tab and near the bottom. Laminated shingles require 4 spots of cement per shingle. After application, press the tab down firmly to start the bond. Be careful not to apply the cement too close to the bottom of the tab. This causes the cement to squeeze out when the tab is pressed down.
CEILING SPOTS
Causes
Spots are caused by leaks in the roof.
Recommendations
- Check attic for leaks in deck.
- Check chimney and vents for cracks in flashing.
- Check rafters for leaks that “travel” away from original source.
- Check eaves for water backing up from ice dams.
- Check roof for damaged shingles.
ROTTING
Causes
Rotting is caused by absorption of moisture by the mat at the core of the shingle. This is a common problem with organic-based shingles.
Recommendations
- Replace with Owens Corning Fiberglas® mat shingles.
MISSING GRANULES
Causes
Normally a certain number of granules will be loose, especially after application. These granules are called “riders” and are a normal result of the manufacturing process. Granule loss does not affect the service life of the shingles unless granules can be seen missing on the surface of the shingles, thus exposing the asphalt or Fiberglas® mat.
Recommendations
- On aging shingles, missing granules indicate a need for replacement.
- Additions and New Construction
- All Exteriors
- Alterations
- Basements
- Bathrooms
- Customer Service
- Customer Stories
- Decks
- Design & Planning Show
- DIY
- Doors
- Educational Resources
- Extreme Makeover Home Edition
- Fashion Show
- General Remodeling
- Green Living
- Handyman Home Services
- Home Decor
- Home Entertainment
- Home Improvement
- Home Improvements
- How to Tips
- In The Community
- Kitchens
- Off-the-Wall Remodeling Stories
- Remodeling
- Resources
- Roofing
- Siding
- Social Media
- Sunrooms
- Tips & Tricks
- Trends
- Windows